Introduction to Aluminum Plate Construction
Aluminum plate construction has emerged as a crucial aspect in modern architecture and various industries. It involves the utilization of aluminum plates, which are thin, flat sheets of aluminum metal, to create structures, facades, and components that offer a multitude of benefits. Aluminum, a silvery-white, lightweight, and highly malleable metal, has gained significant popularity due to its unique combination of properties.
In the construction industry, aluminum plates have become an essential material for several reasons. Firstly, their lightweight nature, approximately one-third the weight of steel, makes them ideal for applications where weight reduction is a priority. This is particularly crucial in high-rise buildings, where the overall weight of the structure can have a significant impact on its foundation and seismic performance. For example, in the construction of modern skyscrapers, the use of aluminum plates in curtain walls and roofing systems helps to reduce the dead load, allowing for more flexible and efficient design.
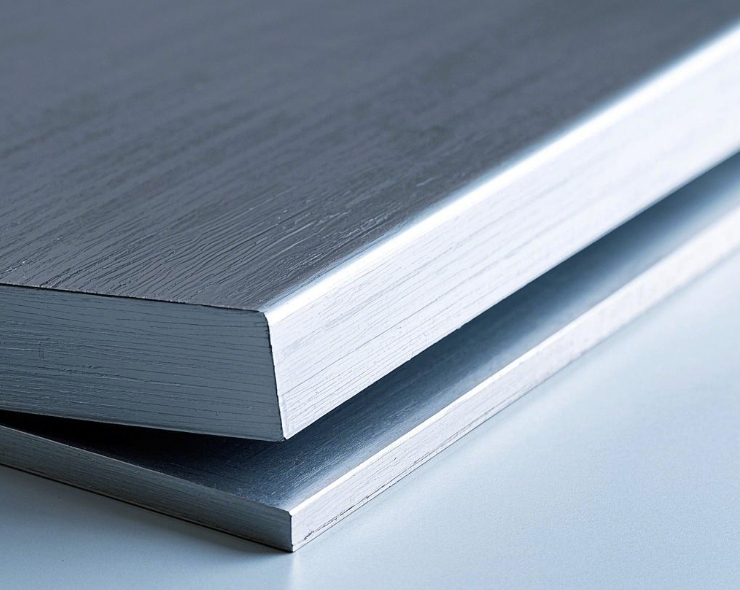
Secondly, aluminum exhibits excellent corrosion resistance. When exposed to air, it forms a thin, protective layer of oxide that prevents further oxidation and deterioration. This property makes aluminum plates highly suitable for outdoor applications and in environments where moisture and harsh weather conditions are present. They can maintain their appearance and structural integrity over an extended period, reducing the need for frequent maintenance and replacement. For instance, aluminum facades in coastal areas or industrial regions with high levels of pollution can withstand the corrosive effects of saltwater and chemical pollutants, ensuring the longevity of the building’s exterior.
Another advantage of aluminum plates is their high thermal and electrical conductivity. This makes them valuable in applications such as heat exchangers and electrical enclosures. In the automotive and aerospace industries, aluminum plates are used in the manufacturing of engine components and aircraft fuselages, respectively, due to their ability to dissipate heat efficiently and their lightweight characteristics, which contribute to improved fuel efficiency and overall performance.
Furthermore, aluminum is a highly malleable and ductile material, allowing it to be easily formed and shaped into a wide variety of complex designs. This flexibility in design enables architects and engineers to create unique and aesthetically pleasing structures. From curved facades to intricate decorative elements, aluminum plates can be fabricated to meet the most demanding design requirements, adding a touch of modernity and elegance to any building project.
In addition to their functional properties, aluminum plates are also recyclable, making them an environmentally friendly choice. Recycling aluminum requires significantly less energy compared to primary production, reducing carbon emissions and contributing to sustainable construction practices. The ability to recycle aluminum plates at the end of their service life further enhances their economic and ecological viability.
Overall, aluminum plate construction has revolutionized the way modern buildings and structures are designed and built. Its versatility, durability, and sustainability have made it a preferred material in a wide range of industries, from architecture and automotive to aerospace and electronics. As technology continues to advance, the potential applications and benefits of aluminum plate construction are only expected to expand, opening up new possibilities for innovative and efficient design solutions.
II. Types of Aluminum Plates Used in Construction
There are several types of aluminum plates available for construction purposes, each with its own unique characteristics, properties, and suitable application scenarios.
1. Alloyed Aluminum Plates
Alloyed aluminum plates are created by combining aluminum with other elements such as copper, magnesium, silicon, or zinc. These alloys are designed to enhance specific properties of aluminum. For example, aluminum-copper alloys (such as 2000 series) exhibit high strength and are often used in structural applications where load-bearing capacity is crucial, like in the framework of aircraft or high-stress components in machinery. Aluminum-magnesium alloys (5000 series) possess good corrosion resistance and weldability, making them suitable for marine applications, such as boat hulls and offshore structures. They can also be used in architectural applications where both strength and resistance to environmental factors are required, such as in roofing and siding systems in coastal areas.
2. Anodized Aluminum Plates
Anodized aluminum plates have undergone an electrochemical process that forms a thick, durable oxide layer on the surface. This oxide layer not only enhances the corrosion resistance of the aluminum but also provides a decorative finish. It can be dyed in a variety of colors, allowing for greater design flexibility. Anodized aluminum is commonly used in architectural facades, curtain walls, and interior decorative elements. For instance, in modern commercial buildings, anodized aluminum panels in different colors can be used to create a unique and visually appealing exterior. The anodized finish also makes it suitable for applications where hygiene is important, such as in food processing plants or hospital interiors, as it is easy to clean and maintain.
3. Aluminum Composite Panels (ACP)
Aluminum composite panels consist of two thin aluminum sheets bonded to a non-aluminum core, usually made of polyethylene or mineral-filled material. ACPs offer a high strength-to-weight ratio, excellent flatness, and good formability. They are widely used in building facades, signage, and interior decoration. In the construction of shopping malls, hotels, and exhibition centers, ACPs are often used to create large, smooth surfaces with a variety of finishes and colors. They can be easily fabricated and installed, reducing construction time and cost. Additionally, the insulation properties of the core material can contribute to energy efficiency in buildings by reducing heat transfer through the walls.
4. Perforated Aluminum Plates
Perforated aluminum plates have a series of holes or perforations of various sizes and patterns. These plates are used for both functional and aesthetic purposes. Functionally, they can provide ventilation, light diffusion, and sound absorption. In industrial buildings, perforated aluminum panels can be used in ventilation systems to allow air to flow while preventing the ingress of debris. Aesthetically, perforated aluminum can create interesting visual effects, especially when combined with lighting. They are often used in interior design, such as in partition walls, ceilings, and decorative screens, to add a touch of elegance and modernity.
5. Brushed Aluminum Plates
Brushed aluminum plates have a surface finish that is created by mechanically brushing the aluminum to produce a parallel pattern of fine lines. This finish gives the aluminum a unique texture and a matte appearance. Brushed aluminum is popular in architectural and interior design applications where a more subdued and sophisticated look is desired. It can be used in door frames, handrails, elevator interiors, and furniture. The brushed finish also helps to hide fingerprints and minor scratches, making it suitable for high-traffic areas where appearance maintenance is important.
III. Preparation Before Aluminum Plate Construction
Before commencing the construction process with aluminum plates, several crucial preparatory steps need to be carried out to ensure the success and quality of the project.
Site Inspection
A comprehensive site inspection is the first and foremost task. This involves carefully examining the construction site to identify any potential issues or challenges that could affect the installation of aluminum plates. The inspection should include an assessment of the existing structures, such as the building framework or support systems, to ensure they are suitable for the attachment of aluminum components. For example, in a building renovation project, the inspector needs to check if the walls and ceilings have the necessary strength and stability to support the weight of aluminum facades or panels. Additionally, the site’s environmental conditions, such as exposure to sunlight, wind, rain, and temperature fluctuations, must be evaluated. This information will help determine the most appropriate type of aluminum plate and installation method. For instance, in areas with high wind speeds, special attention needs to be paid to the fastening and anchoring systems of the aluminum plates to ensure they can withstand the wind loads.
Storage Conditions of Aluminum Plates
Proper storage of aluminum plates is essential to maintain their quality and integrity. Aluminum plates should be stored in a clean, dry, and well-ventilated area, protected from moisture, dirt, and other contaminants. Moisture can cause corrosion, especially in the case of unanodized aluminum plates. The storage area should be free from any sources of water leakage or excessive humidity. It is advisable to store the plates on racks or pallets, keeping them off the ground to prevent contact with damp surfaces. Additionally, the plates should be protected from scratches and dents, which can occur during handling and storage. This can be achieved by using protective coverings or separators between individual plates. For long-term storage, it may be necessary to apply a temporary protective coating to the surface of the plates to prevent oxidation.
Compatibility of Tools and Equipment
Ensuring the compatibility of tools and equipment is vital for efficient and accurate aluminum plate construction. Different types of aluminum plates may require specific tools for cutting, shaping, drilling, and fastening. For example, when cutting alloyed aluminum plates, high-speed steel or carbide-tipped cutting tools are often recommended due to their hardness and ability to withstand the abrasiveness of the alloy. The power and speed settings of cutting and drilling machines need to be adjusted according to the thickness and hardness of the aluminum plates. Incompatible tools can lead to poor cutting quality, excessive burr formation, and even damage to the plates. Moreover, the fastening equipment, such as screws, bolts, and rivets, should be selected based on the type of aluminum plate and the application requirements. The fasteners need to have good corrosion resistance and sufficient strength to hold the aluminum components in place. For instance, in outdoor applications, stainless steel fasteners are commonly used to prevent rust and ensure long-term stability. It is also important to ensure that the tools and equipment are in proper working condition and regularly maintained to avoid any breakdowns or malfunctions during the construction process.
IV. Cutting and Shaping of Aluminum Plates
1. Common Cutting Methods
- Mechanical Cutting:
- Using Saws: Circular saws with carbide-tipped blades are commonly used for cutting aluminum plates. The sharp teeth of the blade can effectively bite into the aluminum, providing a clean cut. For thinner aluminum sheets, a fine-toothed blade is preferred to minimize burr formation. For example, in a workshop dedicated to fabricating aluminum window frames, circular saws are often the go-to tool for cutting the aluminum profiles to the required lengths. The speed of the saw can be adjusted according to the thickness of the plate to ensure a smooth cut. Band saws are also suitable for cutting aluminum, especially for curved or irregular shapes. The continuous band of the saw allows for more flexibility in cutting complex geometries.
- Using Shears: Shearing is a quick and efficient method for cutting straight lines in aluminum plates. Guillotine shears, which operate by a descending blade, can handle relatively thick aluminum plates with ease. They are often used in industrial settings where large quantities of aluminum need to be cut to specific sizes. For instance, in the manufacturing of aluminum roofing sheets, guillotine shears can cut the sheets into the desired widths for installation. However, shearing may cause some deformation at the cut edge, so additional finishing processes might be required for applications where a precise edge is crucial.
- Thermal Cutting:
- Laser Cutting: Laser cutting is a highly precise method that uses a high-powered laser beam to melt or vaporize the aluminum. It is capable of cutting intricate patterns and shapes with minimal heat-affected zones. The focused laser beam can cut through aluminum plates of various thicknesses, and the cutting process can be controlled by computer programs, allowing for high repeatability and accuracy. In the production of perforated aluminum plates with complex hole patterns, laser cutting is often the preferred choice. It can create small, precise holes with smooth edges, enhancing the aesthetic and functional qualities of the plate. Moreover, laser cutting is suitable for cutting aluminum alloys that may be difficult to cut using other methods due to their hardness or composition.
- Plasma Cutting: Plasma cutting utilizes a high-velocity jet of ionized gas to melt and blow away the aluminum. It is effective for cutting thicker aluminum plates, typically up to several inches thick. Plasma cutters are relatively fast and can cut through aluminum with a reasonable degree of accuracy. However, compared to laser cutting, plasma cutting may produce a wider kerf and a rougher cut surface. In construction projects where speed and the ability to cut thick materials are more important than a super-smooth finish, such as in the fabrication of large aluminum structural components for industrial buildings, plasma cutting can be a cost-effective option.
2. Shaping Techniques
- Bending: Aluminum plates can be bent to form various angles and curvatures. This is achieved using press brakes, which apply a controlled force to the plate to create the desired bend. The bending process requires careful consideration of the plate thickness, the type of aluminum alloy, and the radius of the bend. For example, in the manufacturing of aluminum door frames, the edges of the plates are bent at specific angles to form the frame structure. To ensure a smooth and crack-free bend, the correct die and punch settings on the press brake need to be selected, and the aluminum plate may need to be annealed (heated and cooled in a controlled manner) if it is of a harder alloy.
- Rolling: Rolling is used to form aluminum plates into curved or cylindrical shapes. Plate rolling machines can gradually shape the plate by passing it through a set of rollers. This technique is commonly used in the production of aluminum pipes, tubes, and curved architectural elements such as domes or arches. The thickness and width of the aluminum plate, as well as the desired curvature, determine the settings and number of passes through the rollers. For instance, in the construction of a large curved aluminum canopy for a stadium, the aluminum plates are first cut to the appropriate size and then rolled to the required curvature using a heavy-duty plate rolling machine.
- Stamping: Stamping involves using a die and a press to imprint or shape the aluminum plate. It can create embossed patterns, raised logos, or other decorative and functional features. This method is often used in the production of aluminum automotive parts, where specific shapes and textures are required for both aesthetic and functional purposes. For example, the interior trim panels of a car may have a stamping pattern that not only enhances the visual appeal but also provides additional rigidity to the panel. The design of the stamping die needs to be carefully crafted to achieve the desired shape and detail on the aluminum plate.
3. Importance of Precision in Cutting and Shaping
Precision in cutting and shaping aluminum plates is of utmost importance for several reasons. Firstly, in architectural applications, precise cuts and shapes are essential for ensuring proper fit and alignment of the aluminum components. For example, in a curtain wall system, if the aluminum panels are not cut accurately to the required dimensions, gaps may appear between the panels, compromising the building’s energy efficiency and aesthetic appearance. Secondly, in industrial manufacturing, precision is crucial for the functionality and performance of the final product. In the aerospace industry, where aluminum is widely used in the construction of aircraft components, even a slight deviation in the shape or size of a part can affect the aerodynamics and structural integrity of the aircraft. Moreover, precise cutting and shaping can reduce material waste, saving costs and improving overall production efficiency. When aluminum plates are cut and shaped with high precision, there is less need for additional finishing processes such as grinding or filing to correct imperfections, further streamlining the manufacturing process and enhancing the quality of the end product.
V. Surface Treatment of Aluminum Plates
1. Cleaning and Degreasing
The initial step in surface treatment is cleaning and degreasing the aluminum plates. This is essential to remove any dirt, grease, oils, or other contaminants that may have accumulated on the surface during manufacturing, storage, or transportation. These impurities can interfere with the adhesion of protective coatings and compromise the overall performance and appearance of the aluminum plates.
There are several methods for cleaning and degreasing aluminum plates. One common approach is the use of alkaline cleaners. These cleaners contain strong alkaline substances such as sodium hydroxide or potassium hydroxide. They work by saponifying the oils and greases, converting them into water-soluble soaps that can be easily rinsed away. Alkaline cleaners are effective in removing heavy deposits of contaminants and are often used in industrial settings where aluminum plates are heavily soiled. For example, in a manufacturing plant that fabricates aluminum automotive parts, alkaline cleaners may be used to clean the plates before they undergo further processing.
Another method is the use of solvent-based cleaners. These cleaners utilize organic solvents such as acetone, trichloroethylene, or mineral spirits to dissolve and remove the oils and greases. Solvent-based cleaners are particularly useful for removing stubborn or baked-on contaminants. However, they require careful handling due to their flammability and potential environmental hazards. In some cases, a combination of alkaline and solvent-based cleaners may be used to achieve optimal results. For instance, an initial alkaline cleaning may be followed by a solvent rinse to ensure complete removal of all contaminants.
After cleaning and degreasing, thorough rinsing is crucial to remove any residual cleaner from the surface of the aluminum plates. This is typically done using clean water, and in some cases, multiple rinsing steps may be required to achieve the desired level of cleanliness. The rinsed plates are then dried to prevent the formation of water spots or corrosion due to moisture retention.
2. Applying Protective Coatings
Applying protective coatings to aluminum plates is a vital step in enhancing their durability, corrosion resistance, and aesthetic appearance. There are various types of protective coatings available, each offering specific benefits and suitable for different applications.

- Anodizing: Anodizing is a widely used surface treatment method for aluminum plates. It involves an electrochemical process that creates a thick, hard, and porous oxide layer on the surface of the aluminum. This oxide layer provides excellent corrosion resistance and can be dyed in a wide range of colors, offering both protection and decorative options. The anodizing process typically consists of several steps. First, the aluminum plates are cleaned and degreased as described earlier. Then, they are immersed in an electrolytic solution, usually sulfuric acid, and a direct current is passed through the solution. This causes the formation of the oxide layer on the aluminum surface. The thickness of the oxide layer can be controlled by adjusting the process parameters such as the current density, time, and temperature. Once the oxide layer is formed, it can be dyed using organic or inorganic dyes to achieve the desired color. Anodized aluminum plates are commonly used in architectural applications, such as curtain walls, facades, and window frames, as well as in consumer products like electronic housings and kitchen utensils.
- Painting: Painting is another popular method of protecting aluminum plates. It provides a decorative finish while also offering a certain degree of corrosion protection. The choice of paint depends on the specific requirements of the application. For outdoor applications, where the aluminum plates are exposed to harsh weather conditions, weather-resistant paints such as acrylic or polyurethane paints are typically used. These paints have good UV resistance and can withstand moisture, temperature fluctuations, and other environmental factors. Before painting, the aluminum surface needs to be properly prepared by cleaning, degreasing, and often applying a primer. The primer helps to improve the adhesion of the paint to the aluminum surface and provides an additional layer of protection. Painting can be done using various methods, including spray painting, which offers a smooth and even finish, and powder coating, which is a more environmentally friendly option as it produces less volatile organic compounds (VOCs). Powder coating involves applying a dry powder paint to the aluminum surface and then curing it under heat to form a hard and durable finish. Painted aluminum plates are used in a wide range of applications, from building exteriors and industrial equipment to automotive parts and furniture.
- Powder Coating: Powder coating is a dry finishing process that has gained significant popularity in recent years. It involves applying a fine powder of thermosetting polymer resin, such as epoxy, polyester, or a combination of both, to the surface of the aluminum plate. The powder is electrostatically charged and adheres to the electrically grounded aluminum surface. The coated plates are then cured in an oven at a specific temperature and for a certain period of time, allowing the powder to melt and flow, forming a continuous and durable coating. Powder coating offers several advantages over traditional liquid painting. It provides a thicker and more uniform coating, which results in better corrosion resistance and durability. It is also more environmentally friendly as it does not contain solvents and produces less waste. Additionally, powder coating can achieve a wide range of finishes, including smooth, textured, and matte finishes, making it suitable for various aesthetic requirements. Powder-coated aluminum plates are commonly used in architectural elements, such as doors, windows, and railing systems, as well as in the manufacturing of appliances, bicycles, and other consumer products.
- PVDF Coating: PVDF (polyvinylidene fluoride) coating is a high-performance coating system that offers exceptional durability and weather resistance. It is often used in demanding architectural and industrial applications where long-term protection and color retention are crucial. PVDF coatings are available in a variety of colors and finishes and can withstand harsh environmental conditions, including exposure to UV radiation, salt spray, and pollutants. The coating process involves applying a primer layer to the aluminum surface, followed by the PVDF topcoat. The PVDF resin forms a tough and chemically resistant film that provides excellent protection against corrosion and fading. For example, in coastal areas where buildings are exposed to saltwater and strong sunlight, PVDF-coated aluminum plates are frequently used for roofing, cladding, and other exterior applications to ensure the longevity and aesthetic appeal of the structures.
In summary, the surface treatment of aluminum plates through cleaning, degreasing, and the application of protective coatings is essential for maximizing their performance and lifespan in construction and various other industries. These processes not only enhance the corrosion resistance of the aluminum but also allow for greater design flexibility and aesthetic customization, making aluminum plates a versatile and reliable choice for a wide range of applications.
VI. Assembly and Installation of Aluminum Plates
1. Assembly Methods
The assembly of aluminum plates involves joining multiple plates together to form a cohesive structure. There are several methods for assembling aluminum plates, each with its own advantages and suitable applications.
- Welding: Welding is a common method used to join aluminum plates. It creates a strong and permanent bond by melting the edges of the plates and fusing them together. However, welding aluminum requires specific techniques and equipment due to its unique properties. For example, the use of a shielding gas, such as argon, is essential to prevent oxidation during the welding process. Tungsten inert gas (TIG) welding and metal inert gas (MIG) welding are two popular techniques for aluminum. TIG welding offers precise control and high-quality welds, making it suitable for applications where aesthetics and strength are crucial, such as in the fabrication of aluminum furniture or decorative elements. MIG welding, on the other hand, is faster and more suitable for larger-scale projects, like the construction of aluminum frames for industrial buildings or vehicles. When welding aluminum plates, it is important to ensure that the plates are properly cleaned and prepared to achieve good weld penetration and avoid defects such as porosity or cracking.
- Riveting: Riveting is another widely used method for assembling aluminum plates. It involves using rivets, which are mechanical fasteners, to hold the plates together. Riveting offers several advantages, including ease of installation, good resistance to vibration, and the ability to join different thicknesses of aluminum plates. There are various types of rivets available, such as solid rivets, blind rivets, and structural rivets. Solid rivets are commonly used in applications where high strength is required, such as in the construction of aircraft fuselages or bridges. Blind rivets, also known as pop rivets, are convenient for applications where access to only one side of the joint is possible, making them suitable for assembling interior panels or enclosures. Structural rivets are designed to provide enhanced strength and are often used in load-bearing structures. Riveting is a reliable method that does not require the use of heat, reducing the risk of warping or distortion of the aluminum plates.
- Using Adhesives: Adhesive bonding is an increasingly popular method for assembling aluminum plates, especially in applications where a seamless and aesthetically pleasing joint is desired. High-strength adhesives, such as epoxy resins or structural acrylic adhesives, can create strong bonds between aluminum surfaces. Adhesive bonding offers several benefits, including uniform stress distribution, the ability to join complex shapes, and resistance to corrosion. It is also a relatively lightweight joining method compared to welding or riveting, which can be advantageous in applications where weight reduction is important, such as in the aerospace or automotive industries. However, proper surface preparation is crucial for successful adhesive bonding. The aluminum surfaces must be clean, dry, and free from any contaminants or oxides. Additionally, the adhesive must be carefully selected and applied according to the manufacturer’s instructions to ensure optimal bonding strength and durability. In some cases, a combination of adhesive bonding and mechanical fastening, such as riveting or screwing, may be used to provide additional strength and reliability.
2. Installation Procedures on Different Structures
The installation of aluminum plates on different structures, such as walls, roofs, or other parts of a building, requires careful consideration and adherence to specific procedures to ensure proper fit, functionality, and durability.
- Installation on Walls:
- Wall Preparation: Before installing aluminum plates on walls, the wall surface must be prepared. This involves ensuring that the wall is clean, dry, and structurally sound. Any existing paint, plaster, or other coatings should be removed if they are loose or damaged. The wall should be inspected for any irregularities or imperfections, and any necessary repairs or leveling should be carried out. For example, if the wall has cracks or holes, they should be filled and smoothed to provide a flat and stable surface for the aluminum plates.
- Installation of Mounting System: A suitable mounting system needs to be installed on the wall to support the aluminum plates. This can include the use of aluminum framing systems, brackets, or clips. The type of mounting system depends on the size, weight, and design of the aluminum plates, as well as the structural characteristics of the wall. For instance, in the case of large aluminum curtain wall panels, a grid-like aluminum framing system may be installed to provide both support and flexibility for the panels to accommodate thermal expansion and contraction. The mounting system should be accurately positioned and securely fastened to the wall using appropriate anchors or screws. Care should be taken to ensure that the mounting points are evenly spaced and aligned to prevent any distortion or misalignment of the aluminum plates.
- Attachment of Aluminum Plates: Once the mounting system is in place, the aluminum plates can be attached. This can be done by inserting the plates into the framing system or by using clips or screws to secure them to the brackets. The edges of the aluminum plates should be carefully aligned and butted together to create a seamless appearance. If using screws, it is important to use the correct type and size of screws that are compatible with the aluminum plates and the mounting system. The screws should be driven in at the proper torque to ensure a secure attachment without over-tightening, which could damage the plates. In some cases, a gasket or sealant may be used between the plates and the mounting system to provide a watertight and airtight seal, especially in exterior wall applications.
- Finishing Touches: After the aluminum plates are installed, any gaps or joints between the plates should be filled and finished. This can be done using a silicone-based sealant or caulk that is compatible with aluminum. The sealant should be applied neatly and evenly to create a smooth and continuous surface. Additionally, any exposed edges of the aluminum plates may be trimmed or covered with decorative trim pieces to enhance the aesthetic appearance of the installation. Finally, a thorough cleaning should be carried out to remove any dirt, debris, or fingerprints from the surface of the aluminum plates, leaving them clean and shiny.
- Installation on Roofs:
- Roof Assessment and Preparation: Similar to wall installation, the roof must be assessed and prepared before installing aluminum plates. The roof structure should be inspected for its load-bearing capacity to ensure that it can support the weight of the aluminum roofing system. Any damaged or deteriorated roofing materials, such as old shingles or membranes, should be removed. The roof surface should be made clean and smooth, and any protrusions or irregularities should be addressed. For example, if there are existing vents or skylights, they may need to be adjusted or flashed properly to integrate with the new aluminum roofing.
- Installation of Underlayment: An appropriate underlayment is usually installed on the roof deck before laying the aluminum plates. The underlayment serves as a secondary layer of protection against moisture and provides a smooth surface for the aluminum plates to rest on. Common types of underlayment include asphalt-saturated felt, synthetic roofing underlayments, or rubberized membranes. The underlayment should be installed according to the manufacturer’s instructions, with proper overlap and fastening to ensure its effectiveness.
- Laying of Aluminum Roofing Plates: Aluminum roofing plates are typically laid in a specific pattern or sequence, starting from the eaves and working towards the ridge. The plates may have interlocking edges or be fastened using clips or screws. It is important to ensure that the plates are properly aligned and spaced to allow for proper drainage and prevent water pooling. The fastening points should be carefully located and spaced to provide sufficient wind resistance and prevent the plates from lifting or blowing off in windy conditions. In areas with high wind loads, additional fastening or bracing may be required. For example, hurricane clips or straps can be used to secure the aluminum roofing plates to the roof structure more effectively.
- Flashing and Sealing: Flashing is an essential part of aluminum roof installation, especially around roof penetrations, such as chimneys, vents, and valleys. Flashing is made of aluminum or other compatible materials and is used to direct water away from these critical areas and prevent leaks. The flashing should be installed with proper overlap and sealing, using sealants or soldering techniques, depending on the type of flashing and the specific requirements. Additionally, all joints and seams between the aluminum roofing plates and the flashing should be thoroughly sealed to ensure a watertight roof. Regular inspections and maintenance of the roof flashing and seals are important to prevent water infiltration and damage to the building over time.
VII. Quality Control in Aluminum Plate Construction
Quality control is of utmost importance throughout the entire aluminum plate construction process to ensure that the final product meets the required standards, specifications, and performance expectations. There are several key quality control points that need to be closely monitored and managed.
1. Inspection of Raw Materials
Before the construction begins, a thorough inspection of the aluminum plates is essential. This includes checking the material certificates to verify the alloy type, thickness, and other relevant specifications. The surface quality of the plates should be examined for any scratches, dents, or imperfections that could affect the final appearance and performance. For example, in the case of anodized aluminum plates, the thickness and uniformity of the anodized layer should be measured to ensure it meets the desired corrosion resistance and aesthetic requirements. Any defective or non-conforming raw materials should be rejected to prevent quality issues from arising later in the construction process.
2. Dimensional Accuracy Checks
During the cutting and shaping of aluminum plates, precise dimensional accuracy is crucial. Regular measurements should be taken using calibrated measuring tools such as calipers, micrometers, or laser measuring devices. The dimensions of the cut plates should be compared against the design drawings to ensure they are within the acceptable tolerances. For instance, in the fabrication of aluminum window frames, if the dimensions of the frame components are incorrect, it can lead to difficulties in assembly and compromise the integrity of the window, resulting in air or water leakage. In addition to individual plate dimensions, the overall dimensions of assembled structures, such as curtain wall panels or roofing systems, should also be verified to ensure proper fit and alignment.
3. Welding Quality Control
If welding is used in the assembly of aluminum plates, strict quality control measures must be implemented. The welds should be visually inspected for any signs of porosity, cracks, incomplete fusion, or other defects. This can be done using magnifying glasses or non-destructive testing methods such as dye penetrant testing or ultrasonic testing. The welding parameters, including current, voltage, and welding speed, should be recorded and verified to ensure they are within the recommended ranges for the specific aluminum alloy and joint configuration. Additionally, the strength of the welds can be tested by conducting mechanical tests on sample welds, such as tensile or shear tests, to ensure they meet the required strength standards. For example, in the construction of aluminum bridges or structural frameworks, the integrity of the welds is critical to the overall safety and durability of the structure.
4. Surface Treatment Evaluation
After the surface treatment of aluminum plates, the quality of the treatment should be evaluated. For painted or powder-coated surfaces, the thickness, adhesion, and smoothness of the coating should be tested. The thickness can be measured using a coating thickness gauge, and the adhesion can be assessed by performing a cross-cut test or a pull-off test. The color and gloss of the coating should also match the specified standards. In the case of anodized surfaces, the hardness and corrosion resistance of the oxide layer can be evaluated using appropriate testing methods. For example, in the production of aluminum automotive parts with a specific surface finish, any deviation in the coating quality can affect the appearance and durability of the parts, leading to customer dissatisfaction and potential warranty issues.
5. Assembly and Installation Verification
During the assembly and installation of aluminum plates, the quality of the joints and connections should be inspected. Rivets should be checked for proper installation, ensuring they are flush with the surface and have sufficient clamping force. Adhesive bonds should be tested for adhesion strength and integrity. The alignment and spacing of the aluminum plates should be verified to ensure a seamless and aesthetically pleasing appearance. For example, in the installation of aluminum curtain wall panels, any misalignment or gaps between the panels can not only affect the visual appeal but also lead to water infiltration and energy inefficiency. Additionally, the fastening systems used to attach the aluminum plates to the underlying structure should be checked for tightness and stability. In areas prone to earthquakes or high winds, the installation should comply with specific seismic and wind resistance requirements, and the structural integrity of the entire assembly should be verified through engineering calculations and testing.
By implementing a comprehensive quality control program that encompasses all these key points, aluminum plate construction projects can achieve high-quality results, ensuring the durability, functionality, and aesthetic appeal of the final structures. Regular inspections, testing, and documentation of the quality control process are essential to identify and address any potential issues in a timely manner, ultimately leading to successful construction projects that meet or exceed the expectations of clients and stakeholders.
VIII. Maintenance and Repair of Aluminum Plate Structures
Regular maintenance is of paramount importance in prolonging the lifespan of aluminum plate structures. Aluminum is known for its durability and corrosion resistance, but over time, it can still be affected by environmental factors and wear and tear. By implementing a proactive maintenance program, potential issues can be identified and addressed early on, preventing costly repairs and ensuring the continued performance and aesthetic appeal of the structure.
One of the primary maintenance tasks is regular cleaning. Aluminum plates should be cleaned periodically to remove dirt, dust, pollutants, and other contaminants that may accumulate on the surface. This can be done using mild detergents and water, along with soft brushes or cloths. For example, in urban environments where buildings with aluminum facades are exposed to air pollution and traffic emissions, regular cleaning helps to prevent the buildup of grime that could potentially corrode the aluminum or dull its appearance. In coastal areas, where salt spray is a concern, more frequent cleaning is necessary to remove the corrosive salt deposits.
Inspections should also be carried out at regular intervals. These inspections involve visually examining the aluminum plates for any signs of damage, such as scratches, dents, cracks, or loose connections. Additionally, the integrity of the seals and gaskets around the plates should be checked, as these play a crucial role in preventing water infiltration and air leakage. For instance, in a curtain wall system, if the seals around the aluminum panels deteriorate, it can lead to water leaks during rainy seasons, which may damage the interior of the building and affect the structural components over time. Inspections should also include checking the fastening systems, such as screws, rivets, or welds, to ensure they remain secure.
In case of any damages or wear and tear, there are several common repair methods for aluminum plate structures. For minor scratches or surface abrasions, polishing or buffing can often restore the appearance of the aluminum. This involves using fine abrasive materials to gently remove the damaged layer and smooth the surface. If there are small dents, they can sometimes be repaired using specialized tools that apply pressure to pop the dent back into place, especially if the aluminum plate is relatively thin and malleable.
For more significant damage, such as cracks or holes, weldi